


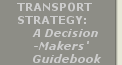 
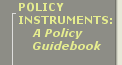



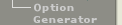
|
Taxonomy and description
Terminology & Technology
Road freight fleet management systems generally consist of a number of
telematic systems which use remote devices on both freight vehicles and
trailers to control and monitor freight operations and present this data
in a useable format to freight managers, either as real time data or static
data. The effective use of these systems can lead to improvements in fleet
efficiency and productivity via reductions in fleet mileage, operational
costs and fuel consumption. In addition effective fleet management can
lead to improvements in safety and a reduction in the environmental impact
of freight fleets. To maximise the impact of road freight fleet management
systems careful fuel management, driver training and training in the use
of the freight fleet system should be seen as being essential. In a Good
Practice Guide (341) issued by the Department for Transport (DfT) (2003)
seven potential functions of fleet management systems were outlined. The
full list is outlined below, but certain applications will suit different
hauliers more depending upon the size of their fleets and the type of
operations they carry out.
- Data on the performance of both drivers and vehicles;
- Vehicle tracking systems;
- Text messaging communication
- Trailer tracking;
- Paperless manifest and proof of delivery;
- Traffic information and
- On-board navigation systems.
With over 70 companies offering freight fleet tracking systems it is impossible to outline all the possible fleet management
systems on offer in the market place. However, each of fleet management system offers some combination of the following
components:
a) Hardware
This is equipment that is fitted to the vehicle/trailer and into the haulier's office to collect data. The basic on-board
hardware will usually include the following technology:
- On-board computer - a small device that collects and stores data from the vehicle and/or reads a Global Positioning
System (GPS) and controls data communications;
- Fuel flow meter - this measures the amount of fuel used by the engine and provides an important input to the
on-board computer, especially when better fuel management is an objective;
- GPS Receiver - usually a passive device (such as a radio receiver). It reads signals from up to 12 satellites
(but needs a minimum of 3) and calculates a vehicle's surface position to within 10 to 20 metres or 1 to 5 metres if
differential GPS is used;
- Communication Module - a sophisticated box of electronics and software. It acts as the gateway between the
vehicle equipment and the communications network;
- Driver Terminal/Keypad - Usually made up of a small screen and keyboard/key pad though increasing portable units are being used;
- Navigation module - an in cab display that provides turn by turn instructions (graphically, verbally or both);
- Trailer tracking - a dedicated unit for trailers that are self contained and include a GPS receiver, communications modules,
control electronics and batteries for when the trailer isn't connected to the vehicle; and
- Other equipment - driver coaching devices (to promote more economic
driving), delivery note and invoice printers, bar code wands and terminals
that can record customer signatures electronically for proof of delivery
applications.
b) Data Transfer
This is how data collected from the vehicle/trailer is transmitted to the office. For those hauliers who wish to have real
time information the most common solutions are via the mobile phone network (GSM) or SMS. Some solutions offer satellite data
communications. If real time data is not required (e.g. fuel usage) then data can be downloaded when the vehicle returns to its
depot using wireless or direct cable connection.
The data flow is likely to be both ways between the vehicle and the vehicle control centre. The potential flow of data to the
vehicle includes the following:
- Manifest - drops/addresses/route;
- Manifest modifications en route;
- Text messages;
- Voice - operations/turn by turn navigation;
- Vehicle disabling commands;
- Traffic status en route;
- Route recommendation and modification;
- System configuration/calibration.
The potential flow of data from the vehicle to the office includes the following:
- Vehicle or trailer location at calibrated intervals or upon request;
- Vehicle location when entering or leaving a 'geo-fence' (virtual fence
placed around a destination to inform a depot of a vehicles imminent
arrival);
- Vehicle location when panic alarm triggered;
- Vehicle location when fridge or other alarm triggered, e.g. off route;
- Confirmation of delivery specified in electronic manifest;
- Proof of delivery - electronic signature;
- Consignment tracking - barcode etc;
- Text messages;
- Driver identification;
- Fuel consumption - trip/totals;
- Driving style - speed/revs/idling/braking;
- Timed trip data - start, stops, average speed, distance;
- Door openings - time/ duration/ location;
- PTO activity;
- Driving hours;
- Engine performance - e.g. temperatures;
- Trailer identification and mileage.
c) Management Software
This is how the data collected is transformed into useful information to assist the haulier in his management of the fleet.
This may take many forms, including a custom report containing key performance indicators/information, mapping and text messaging
facilities or an order tracking system linked with ordering and accounting software. The key feature of the software is that it
provides the haulier with all the information they require to help manage the fleet.

|